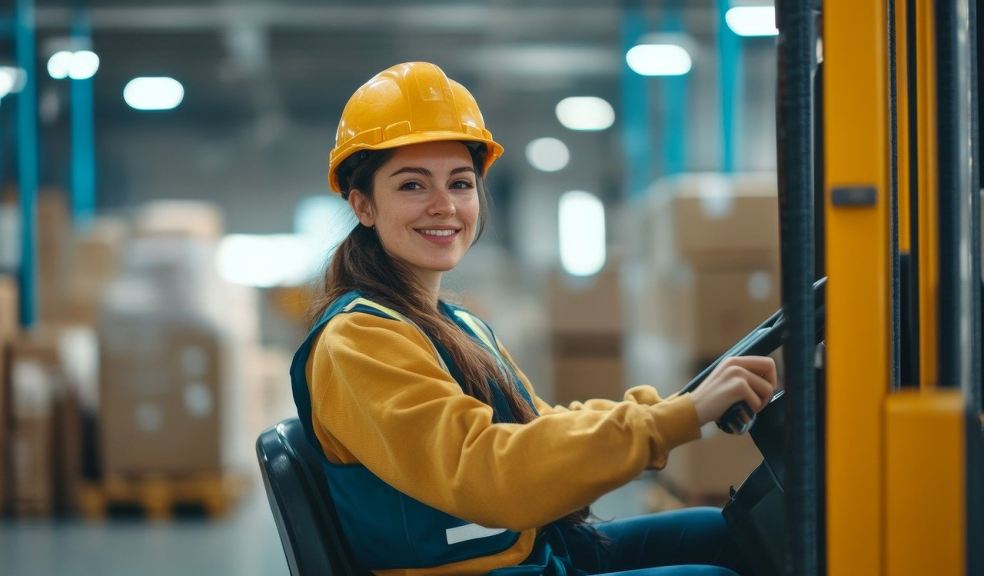
Workplace Safety: How to Stay Protected and Avoid Common Accidents
Workplace safety is a critical concern for both employers and employees across all industries. In the UK, recent data from the Health and Safety Executive (HSE) shows that while great strides have been made in improving workplace safety, there’s still work to be done. In 2022/23, there were an estimated 561,000 workers who sustained non-fatal injuries, and tragically, 135 workers lost their lives due to work-related incidents.
These statistics underscore the importance of ongoing efforts to enhance workplace safety. This guide aims to provide practical advice on:
- Identifying and mitigating common workplace hazards
- Creating a robust culture of safety in the workplace
- Understanding and properly using personal protective equipment
By focusing on these areas, we can work together to reduce workplace accidents and ensure everyone returns home safely at the end of each workday.
Common Workplace Hazards
Slips, trips, and falls remain one of the most prevalent causes of workplace injuries across various industries. These accidents can occur due to wet or uneven surfaces, poor lighting, or obstacles in walkways. To minimise these risks, it’s crucial to maintain clean and tidy work areas, ensure proper lighting, and address any flooring issues promptly.
Ergonomic issues, particularly in office environments, can lead to long-term health problems. Poor posture, repetitive motions, and improperly adjusted workstations can result in musculoskeletal disorders. Addressing these concerns through proper ergonomic assessments and adjustments can significantly reduce the risk of chronic injuries.
Chemical exposures pose significant risks in many industries, from manufacturing to healthcare. Proper handling, storage, and disposal of hazardous substances are essential. This includes ensuring adequate ventilation, using appropriate containment measures, and providing employees with necessary protective equipment and training.
Machinery accidents, while less common, can result in severe injuries. These often occur due to inadequate guarding, lack of proper training, or failure to follow lockout/tagout procedures during maintenance. Regular machinery inspections, comprehensive training programmes, and strict adherence to safety protocols are crucial in preventing these incidents.
Creating a Culture of Safety
Management plays a pivotal role in promoting safety within the workplace. Leaders must demonstrate a genuine commitment to safety through their actions and decisions. This includes allocating resources for safety initiatives, actively participating in safety meetings, and consistently enforcing safety policies.
Employee training and education form the foundation of a strong safety culture. Regular safety training sessions should cover general workplace safety as well as job-specific hazards. These sessions should be engaging and interactive, encouraging employees to ask questions and share their experiences.
Implementing safety protocols and procedures is essential, but it’s equally important to ensure these are practical and consistently followed. Involve employees in developing and refining these procedures to ensure they’re relevant and effective. Regular reviews and updates of safety protocols help keep them current with changing workplace conditions and emerging best practices.
Personal Protective Equipment (PPE)
Personal Protective Equipment is often the last line of defence against workplace hazards, making its proper use crucial. The types of PPE required vary widely across industries. In construction, this might include hard hats, safety glasses, and steel-toed boots. In healthcare settings, gloves, masks, and eye protection are common. Manufacturing environments might require hearing protection and specialised clothing.
Proper use and maintenance of PPE are just as important as having the right equipment. Employees should be trained on how to correctly wear and adjust their PPE. Regular inspections and maintenance schedules should be established to ensure equipment remains in good condition. Damaged or worn PPE should be replaced promptly.
Ensuring compliance with PPE regulations is a shared responsibility. Employers must provide appropriate PPE and ensure it meets relevant safety standards. Employees have a duty to use the provided PPE correctly and consistently. Regular audits and spot checks can help maintain high levels of compliance. Remember, PPE is most effective when it’s part of a broader safety strategy that includes hazard elimination and engineering controls.
Emergency Preparedness
Developing a comprehensive emergency action plan is crucial for every workplace. This plan should outline procedures for various emergencies, including fires, natural disasters, and medical emergencies. It should clearly define evacuation routes, assembly points, and the roles and responsibilities of key personnel during an emergency.
Conducting regular safety drills is essential to ensure all employees are familiar with emergency procedures. These drills should be varied to cover different scenarios and conducted at different times to account for shift workers. After each drill, gather feedback and use it to refine and improve your emergency response procedures.
First aid and emergency response training can make a critical difference in the event of an accident or medical emergency. Ensure that a sufficient number of employees are trained in first aid and CPR. Consider installing automated external defibrillators (AEDs) in easily accessible locations and train staff in their use. Remember to regularly check and restock first aid supplies and ensure emergency contact information is up to date.
By focusing on these areas, workplaces can significantly enhance their safety measures and be better prepared to handle emergencies when they arise. Remember, emergency preparedness is an ongoing process that requires regular review and updates to remain effective.
Reporting and Addressing Safety Concerns
Establishing a robust system for reporting hazards is crucial for maintaining a safe workplace. This system should be easily accessible to all employees and allow for anonymous reporting if desired. It could involve a dedicated safety hotline, an online reporting tool, or regular safety walk-throughs where employees can point out potential hazards.
The importance of near-miss reporting cannot be overstated. Near-misses are valuable learning opportunities that can help prevent more serious incidents in the future. Encourage employees to report these incidents without fear of repercussion. Create a culture where near-miss reporting is seen as a positive contribution to workplace safety rather than a negative reflection on anyone’s performance.
Following up on safety reports and concerns is essential to maintain trust in the reporting system. Establish a clear process for investigating reported hazards or concerns and communicate the outcomes to employees. Even if a reported issue cannot be immediately addressed, explain the reasons and any planned future actions. This transparency helps employees feel heard and encourages continued engagement in safety efforts.
Accidents and Injury at Work Claims
Understanding your rights as an employee is crucial when it comes to workplace safety and injury claims. In the UK, workers have the right to work in environments where risks to health and safety are properly controlled. If you’re injured at work, you have the right to make a claim for compensation without fear of losing your job.
If you’re injured at work, there are several important steps to take. First, seek medical attention immediately, even for seemingly minor injuries. Report the incident to your supervisor as soon as possible and ensure it’s recorded in the workplace accident book. Gather evidence if you can, including photographs of the accident scene and contact details of any witnesses.
Working with solicitors like Hudgell Solicitors can provide valuable support in navigating the complex process of workplace injury claims. These legal professionals can help you understand your rights, gather necessary evidence, and negotiate with employers and insurance companies on your behalf. They can also ensure you’re aware of time limits for making a claim and help you pursue the appropriate compensation for your injuries and any resulting financial losses.
Staying Updated on Safety Regulations
Industry-specific safety standards are continually evolving, and staying informed about these changes is crucial for maintaining a safe workplace. In the UK, the Health and Safety Executive (HSE) is the primary source for workplace safety regulations across various industries. Regularly check their website for updates relevant to your sector.
There are numerous resources available for keeping informed about safety updates. Professional associations often provide industry-specific safety information through newsletters, webinars, and conferences. Consider joining relevant safety organisations or subscribing to safety-focused publications. Many of these resources offer practical advice on implementing new safety measures.
Regular safety audits and inspections are vital for ensuring ongoing compliance with safety regulations. These should be conducted by trained personnel and involve a thorough examination of the workplace, equipment, and practices. Use these audits to identify areas for improvement and to verify that existing safety measures are effective. Remember, safety audits are not about finding fault, but about continuously improving workplace safety for everyone.