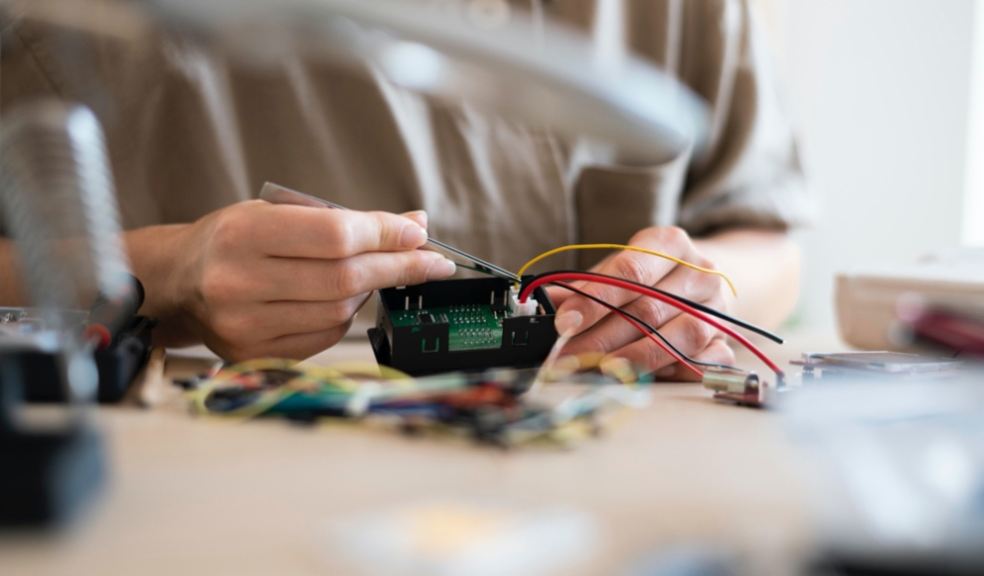
What is a Bill of Materials for Electronics Manufacturing Services?
A Bill of Materials (BOM) is an essential part of product documentation, prepared as a complete list of all components and materials, as well as their comprehensive descriptions, including information on manufacturers, identification numbers, and quantity, used to manufacture a particular electronic item.
To create a BOM, an original equipment manufacturer (OEM) needs the assistance of a qualified product design team. While this task requires a certain effort, it can greatly streamline the manufacturing process. This article will show you how.
Why should you use a BOM for EMS?
A BOM plays a critical role in both manufacturing processes and quality control procedures. While its main role is to help electronics manufacturers identify and procure the components and materials needed for device production, there are many other tasks that a BOM helps accomplish.
For example, BOM can assist EMS providers in inventory management if integrated with an enterprise resource planning (ERP) system since it can be used as a foundation for an overview of component availability and usage, which helps EMS providers to plan and maintain appropriate inventory levels.[RB1] A BOM also serves as part of the assembly instructions, as it can contain additional information such as reference designators to assist in the manufacturing process.
A BOM is also an essential document for quality control because it contains component specifications. A BOM helps avoid scenarios where incompatible materials are used for production. In addition, the BOM is necessary to ensure product traceability, which in turn is one of the key quality standard requirements for certain industries, such as medical electronic device production.
What information should be included in the component specification?
Each component on your BOM should be uniquely identified. An MPN (Manufacturer Part Number) should not be incomplete or ambiguous. You should define the quantity requirements for manufacturing a single complete product. Remember to specify all items separately for each production step in which they are used.
An Approved Vendor List (AVL), which provides information on component manufacturers officially approved by the client, should also be on your BOM.
One more crucial point is the reference designator (RefDes) for mounting the component in the right place on the PCB.
Make sure to list alternative components that can be used if the originally planned components are unavailable.This practice is critical for sustaining continuous production when some materials are not available.
Tips for creating a bill of materials
Here is a short guide to creating an effective BOM from a leading Polish EMS provider Assel.
A convenient way to create your BOM is to use spreadsheet programs such as Excel, as they maintain a clear structure of a list and make editing easier. It is recommended to place the components in one column and all related information in the columns next to it.
A good practice is to create an addition to your BOM with the manufacturing steps. Another document should be attached to the BOM to provide comprehensive information on manufacturing and packaging processes with detailed descriptions of the materials used, as well as graphics to visualize the final product. Consider attaching a sample.
If the selected product’s components are to be provided by the dedicated vendors of your choice, or you have special pricing for individual components agreed with the manufacturer or distributor for your project, please include such information in BOM as well.
Make sure to always provide the latest version of a BOM to your contract electronics manufacturer or you risk disrupting production. The best practice for managing a BOM is to update the same file rather than creating a new one after each update.
Maintain your BOM for optimized production
Every OEM should consider creating a Bill of Materials that is worth the time and effort, as it can effectively support the work of a contract electronics manufacturer like Assel, which uses this documentation for planning, procurement, production, and quality control. To learn more about working with Assel, visit asselems.com.